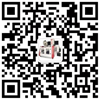
微信公众号
数控机床抖动是日常维修常见的一种故障类型,造成故障的原因十分普遍,且不易判断查找。对数控龙门铣床X轴抖动故障的分析与处理过程进行了详细阐述,并介绍了数字控制机床蜗杆与蜗母条配合间隙的调整方法及相关需要注意的几点,为该类传动方式的数控机床抖动故障处理提供了经验借鉴。
数控龙门钻铣床是一种先进的加工设施,它采用了全铸造床身和焊接床身的设计,以提供更强大、稳定和精确的加工能力。本文将重点介绍全铸造床身和焊接床身的优点,并解释该产品的相关功能。
1. 高刚性:全铸造床身的材料均匀,结构稳定,可承受高负荷和剧烈振动,来保证了高精度的加工。
2. 减少振动:全铸造床身拥有非常良好的吸震性能,能有实际效果的减少工艺流程中的振动,提高工件的表面上的质量和加工精度。
3. 长寿命:全铸造床身的耐磨性和抗腐蚀性能优秀,可以有明显效果地延长设备的常规使用的寿命,降低维修和更换零部件的成本。
1. 轻量化:焊接床身相比全铸造床身更轻巧,便于搬运和安装,节约空间,提高生产效率。
2. 精确度高:焊接床身在生产的全部过程中能够直接进行精确的尺寸控制,确保各个部件的精度和配合度,提供更高精度的加工能力。
3. 成本低:焊接床身的制造成本相比来说较低,降低了产品的售价,提高了市场竞争力。
新设备在安装调试后,X轴一直存在声音大、轻微抖动现象,厂家也多次来优化调整,但效果不理想。随着设备继续运行,抖动现象也慢慢变得严重,有时还会出现轮廓误差监控报警,已严重影响产品的加工精度。
蜗杆箱固定在机床床身中部,与工作台进给箱传动轴相连接,通过蜗杆与工作台面下方的蜗母条啮合,使工作台(X向)移动。
蜗杆箱中的蜗杆是静压蜗杆,运行时液压系统恒定的压力油注入蜗杆与蜗母条的啮合齿面,形成一定厚度的高强度静压油膜,使蜗杆与蜗母条形成无摩擦传动,因而传动效率和精度高,无磨损,寿命长。
油腔开设在蜗杆齿侧面上。静压蜗杆采用双联泵供油,即由双联泵引出流量相等的两条油路,分别向蜗杆左右两侧油腔供油。
静压蜗杆除有一套静压供油泵组外,还有一套静压蜗杆预冲油系统,当蜗杆与蜗母条的油腔脱离啮合区时,静压油路断开,预冲油接通,使非啮合的油腔仍充满油,防止油路混入空气,以提高蜗杆油膜的静压刚度,保证承载力度。静压蜗杆采用轴向配油的形式。静压蜗杆结构如图2所示。
根据对X轴传动机构的工作原理分析后认为,造成X 轴抖动的原因有很多,如工作台静压压力低,蜗杆静压压力低,蜗杆制动没有打开,工作台压板调整间隙过小,伺服电动机本身故障,检测单元故障,伺服参数设置不当,以及蜗杆与蜗母条间隙不当等。
为了避免大量盲目的拆卸,提高维修效率,首先对工作台静压压力、蜗杆静压压力、蜗杆制动压力、X轴检测单元及伺服控制参数进行全方位检查,无异常。然后脱开X轴伺服电动机,将X轴改为半闭环运行试车,电动机运转正常,无抖动现象,排除伺服电动机本身问题。分析可能会引起本次故障的主要影响因素为工作台压板调整间隙过小或蜗杆与蜗母条间隙不当。
(1)工作台压板调整间隙过小工作台采用闭式静压导轨,下方共有8块压板,机床安装时压板间隙调整过小,将会造成工作台浮起量不够,出现X轴抖动故障。
(2)蜗杆与蜗母条间隙不当蜗轮与蜗母条两者之间是靠恒定的压力油形成静压油膜,使蜗轮蜗杆实现无摩擦传动,如蜗轮与蜗母条间的间隙过小,则会造成静压油膜压力不稳定,出现抖动故障。
通过查阅机床有关的资料,工作台压板与导轨的间隙应控制在0.05mm内。间隙过小,工作台的静压浮起量不够,机床加工时会产生抖动现象;间隙过大,机床又没办法保证自身刚性要求。
拆开X轴两边的防护罩,将工作台静压关掉,使用塞尺逐个对压板与导轨的间隙进行全方位检查,发现8块压板与导轨的间隙都在允许范围0.05mm内。
通过调整蜗杆箱安装座下方的垫片厚度,可实现蜗杆与蜗母条间隙的调整。因蜗杆箱位于床身的中间位置,故调整时需将工作台移开,露出蜗杆箱,然后拆出垫片实现间隙调整。具体的实施步骤如下。
1)将PLC状态点DB99.DBX1.1设置1,DB99.DBX1.2设置0,X轴由全闭环改为半闭环,然后断开蜗杆静压泵空开,修改PLC程序,屏蔽其报警功能。关掉蜗杆静压主要是为了更好地检测出蜗杆与蜗母条的实际间隙。
2)准备好百分表,对蜗杆与蜗母条的实际间隙进行仔细的检测。用手轮先正向慢速移动一段距离(注意一定要慢,因为蜗杆静压关掉了,蜗杆、蜗母条之间无静压油膜,同时移动时还需监控X轴的电流),然后反向移动0.01mm,测出的间隙为0.03mm。测出的蜗杆与蜗母条间隙偏小,间隙正常值应为0.06mm。
4)将X轴硬限位开关和两边的电缆拖链固定支座拆掉,然后打开蜗杆静压,使X轴正向移动,直至蜗杆与蜗母条快脱开时,在PLC程序屏蔽X轴后多头泵的压力报警。因为工作台往后端移动时有一段静压压力建立不起来。
5)关停蜗杆静压泵,在工作台的正向位置安装一个手动葫芦,最后一段距离内用手动葫芦拉着工作台轻微受力,同时正向缓慢转动蜗杆,直至蜗杆与蜗母条全部脱开。
6)拆掉蜗杆箱8个定位销和14个M17内六角固定螺钉,然后在蜗杆箱两端的下方各放置一个螺纹顶,用两个螺纹顶将蜗杆箱轻微顶起,拿出蜗杆箱与床身之间的垫片,共4块,做好记号,方便后面安装。
7)可根据蜗杆与蜗母条的夹角确定垫片厚度调整的具体数值,最终计算结果是需要将拿出来的垫片磨掉0.3mm,这样做才能够增加蜗轮蜗杆的间隙0.03mm左右。
8)垫片加工好,按记号进行装配,打入蜗杆箱定位销,拧紧固定螺钉。空转蜗杆,用手将蜗杆上面的脏东西清理干净。
9)连接蜗杆与蜗母条,将正向蜗杆端没有齿的半圈转至朝上,用千斤顶将工作台慢慢往负向顶,直至工作台蜗母条前端面与蜗杆齿的端面接触,这时千斤顶轻微受力,机床开启蜗杆静压,慢慢转动蜗杆,使蜗杆与蜗母条连接上。之后缓慢移动X轴,监控其电流是不是正常和有无异响。
10)将上述步骤拆掉的部件,按之前做的记号依次装好,同时按上述蜗杆与蜗母条间隙的检测的新方法,对其反向间隙进行仔细的检测,反向间隙为0.06mm,检测正常。然后将X轴改为全闭环,将PLC屏蔽的报警全部打开,编辑循环程序对X轴的运转状态进行全方位检查,试车正常,抖动故障消除。
蜗母蜗杆传动机构作为大型数控龙门镗铣床的重要物理运动部件,其加工精度、装配精度和控制精度要求比较高;同时蜗母蜗杆机构作为机床进给轴的动力传递方式,由于其需要承受主要的切削力和不规则振动,因此故障率相对较高。
此次故障处理耗时较长,同时又是机械、液压和电控等一系列问题的结合,处理此类故障时需要对传动机构的机械部分、液压控制部分和PLC控制管理系统有一定水平的认知。在充分分析故障和了解机床结构后,对蜗杆与蜗母条的间隙进行仔细的检测和调整,可有效消除机床抖动故障现象。
微信公众号